Система
М-Мотроник
1.Общее
устройство системы
Система М-Мотроник
включает в себя все элементы, необходимые для управления двигателем с впрыском
во впускной трубопровод и традиционной дроссельной заслонкой. На рис. 137
показан пример системы М-Мотроник. Ее диапазон применения определяется
требованиями в отношении мощности двигателя, а также ограничениями, накладываемыми
со стороны законодательства на токсичность отработавших газов. Центральным
узлом управления системы М-Мотроник является блок управления двигателем 21, который
регистрирует все входящие сигналы и вырабатывает сигналы управления,
поступающие на исполнительные устройства.
На протяжении истории эволюции системы Мотроник возникли
поколения вариантов этой системы (например, М1, М3, М7), которые отличаются в
первую очередь содержанием аппаратных средств.
Существенными
отличительными по знаками являются микроконтроллеры, периферийные модули и
модули оконечных каскадов (набор чипов). Вариант аппаратных средств,
возникающие в соответствии с требованиями различных производителей автомобилей,
отличаются идентификационными кодовыми номерами производителей автомобилей
(например, М4.3).

Рисунок
137 – Элементы электронного управления работой двигателя с помощью системы
М-Мотроник:
1 – абсорбер с
активированным углем; 2 – диагностический модуль негерметичности топливного
бака; 3 – клапан регенерации; 4 – насос подачи дополнительных порций воздуха; 5
– клапан подачи дополнительных порций воздуха; 6 – датчик массового расхода
воздуха со встроенным датчиком температуры; 7 – датчик давления во впускном
трубопроводе; 8 – впускной трубопровод с изменяемой геометрией (с заслонками
управления); 9 – топливная рейка; 10 – топливная форсунка; 11 – исполнительные
устройства и датчики изменения фаз газораспределения; 12 – катушка зажигания с
установленной свечой зажигания; 13 – датчик фаз; 14 – датчик углового положения
дроссельной заслонки; 15 – регулятор частоты вращения коленчатого вала на
холостом ходу; 16 – дроссельная заслонка; 17 – клапан рециркуляции отработавших
газов; 18 – датчик детонации; 19 – датчик температуры в системе охлаждения
двигателя; 20 – лямбда-зонд перед каталитическим нейтрализатором; 21 – блок
управления двигателем; 22 – датчик частоты вращения коленчатого вала; 23 –
трехкомпонентный каталитический нейтрализатор (в ряде случаев используют
отдельные основной и вспомогательные каталитические нейтрализаторы); 24 –
диагностический интерфейс; 25 – лампа-индикатор неисправностей; 26 – интерфейс
блока управления иммобилайзером автомобиля; 27 – интерфейс блока управления
трансмиссией; 28 – интерфейс бортового контроллера связи; 29 – топливный бак;
30 – датчик давления в топливном баке; 31 – топливопровод; 32 – модуль,
встроенный в топливный бак, содержащий электроприводной насос, топливный фильтр
и регулятор давления топлива; 33 – лямбда-зонд за каталитическим нейтрализатором
2.Элементы
системы воздухоподачи
Дроссельная
заслонка
Педаль газа соединена с дроссельной заслонкой 16 (рис.137)
рычажным механизмом или тросиком. Положение дроссельной заслонки определяет
степень открытия отверстия для впуска воздуха. Это позволяет управлять массовым
расходом воздуха, проходящего в цилиндры через впускной трубопровод.
Регулятор
частоты вращения коленчатого вала на холостом ходу
С помощью регулятора
частоты вращения коленчатого вала на холостом ходу 15 (рис.137) определенный
поток воздуха может направляться в обход дроссельной заслонки. Это позволяет
удерживать частоту вращения коленчатого вала на режиме холостого хода на
постоянном уровне (регулировка частоты вращения коленчатого вала на холостом ходу).
В этом случае блок управления двигателем изменяет степень открытия байпасного
канала.
Датчики
определения нагрузки двигателя
Нагрузка двигателя
является важным рабочим параметром системы электронного управления двигателем.
Она является мерой наполнения воздухом цилиндра на момент сгорания и,
следовательно, массы всасываемого воздуха. Это основной параметр для расчета
времени впрыскивания топлива.
Существуют различные
возможности определения нагрузки на двигатель. В системах М-Мотроник используются
следующие датчики:
·
измеритель объемного расхода воздуха;
·
термоанемометрический измеритель
массового расхода воздуха;
·
термоанемометрический пленочный датчик
массового расхода воздуха;
·
датчик давления во впускном
трубопроводе;
·
датчик положения дроссельной заслонки.
В зависимости от
конфигурации системы Мотроник могут использоваться лишь отдельные датчики или
комбинации датчиков.
Датчик давления во
впускном трубопроводе (рис.141)
Датчик давления во
впускном трубопроводе (7, рис.137) соединен с впускным трубопроводом пневматическим
путем и, таким образом, определяет абсолютное давление во впускном
трубопроводе. На основе данных об этом давлении, температуре всасываемого
воздуха и частоте вращения коленчатого вала может быть рассчитана масса
воздуха, поступающего в цилиндры двигателя.
Датчик состоит из
измерительного элемента и камеры для схемы обработки сигнала. Обе этих части
расположены на общей керамической подложке (рис.141).

Рисунок
141 – Толстопленочный датчик давления:
1 –
подвод измеряемого давления; 2 – измерительный элемент давления; 3 –
герметизирующая перегородка; 4 - схема оценки сигнала; 5 – толстопленочный
гибрид на керамической подложке; p –
измеряемое давление
Датчик углового
положения дроссельной заслонки (рис.143)
В датчике углового
положения дроссельной заслонки (14, рис.137) используется потенциометр, который
определяет положение дроссельной заслонки и вырабатывает аналоговый сигнал
напряжения. Этот сигнал обычно используется только как вспомогательный сигнал
нагрузки. Он дает дополнительную информацию для реализации динамических функций
и детектирования диапазона рабочих режимов двигателя (холостой ход, частичная
нагрузка, полная нагрузка) и является дублирующим сигналом при выходе из строя
основного датчика нагрузки двигателя.
Если датчик углового
положения дроссельной заслонки используется в качестве основного датчика
нагрузки двигателя, то требования к точности измерений возрастают. Более
высокая точность достигается за счет использования двух потенциометров и улучшенных
подшипников поворотного рычага.
Рычаг движка потенциометра
(рис.143), соединенный механически с осью дроссельной заслонки и щеточными
ползунами, перемещается по соответствующим резистивным дорожкам. При этом он преобразует
поворот оси дроссельной заслонки в пропорциональное этому соотношение напряжений.
Рабочее положение равно
значению UV = 5 В. Электроподсоединение движка чаще всего осуществляется
через вторую дорожку потенциометра с одинаковой поверхностью, но с подложкой из
материала, обладающего малым сопротивлением (рис.143).
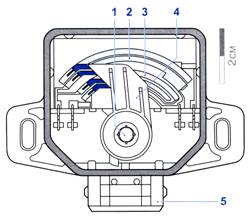
Рисунок
143 – Датчик положения дроссельной заслонки:
1 – ось
дроссельной заслонки; 2 – резистивная измерительная дорожка 1; 3 – резистивная
измерительная дорожка 2; 4 – рычаг с контактным движком; 5 – электрическое
соединение
3.Элементы
топливной системы
Топливный насос с электрическим
приводом
Топливный насос с электрическим приводом (32,
рис.137) прокачивает топливо из топливного бака 29 через топливопроводы 31 под
давлением, определяемым регулятором.
Топливный насос с электрическим приводом (рис.145) состоит
из:
·
торцевой крышки А, в которую, если требуется, встраиваются
элементы для устранения радиопомех от работы системы зажигания;
·
электродвигателя В;
·
элемента насоса С, выполненного как поршневой или центробежный.

Рисунок
145 – Конструкция топливного насоса с электрическим приводом на примере
центробежного насоса:
1 – электрический
разъем; 2 – гидравлический соединительный разъем (выпуск топлива); 3 – обратный
клапан; 4 – графитовые щетки; 5 – якорь двигателя с постоянным магнитом; 6 –
рабочее колесо насоса; 7 – подача топлива
Давление растет по длине канала 7 за счет обмена
импульсами между лопатками рабочего колеса и частицами жидкого топлива. Это
приводит к спиралевидному вращению объема жидкого топлива, захватываемого
рабочим колесом и в каналах.
В центробежном вихревом насосе канал окружают
лопатки рабочего колеса по все его окружности. В центробежном открыто-вихревом
насосе оба канала располагаются с двух сторон рабочего колеса рядом с его
лопатками.
Центробежные насосы создают мало шума, т.к. рост
давления осуществляется непрерывно и почти без пульсаций. Конструкция
центробежных насосов по сравнению с поршневыми является заметно упрощенной.
Если в начале истории электронного управления
впрыском топливный насос с электрическим приводом устанавливался исключительно
снаружи топливного бака в топливопроводе последовательно, то сегодня чаще всего
он размещается в топливном баке. При этом он является элементом блока, установленного
в топливном баке, который также называется модулем подачи топлива (рис.147).
Этот модуль содержит следующие элементы:
·
фильтр предварительной очистки топлива 6;
·
датчик уровня топлива в топливном баке 5;
·
электрические и гидравлические соединительные разъемы;
·
специальный бачок для резервного топлива, используемого при
движении на резких поворотах (чтобы избежать перерывов в подаче топлива).

Рисунок
147 – Блок топливного насоса:
1 – топливный фильтр;
2 – топливный насос с электрическим приводом; 3 – струйный насос; 4 – регулятор
давления топлива; 5 – датчик уровня топлива в топливном баке; 6 – фильтр
предварительной очистки топлива
Этот модуль чаще всего заполняется топливом с
помощью струйного насоса 3 или отдельной добавочной ступенью топливного насоса
с электрическим приводом 2.
Топливный
фильтр
Топливный фильтр
задерживает загрязнения, содержащиеся в топливе, защищая от них узлы системы
впрыска. Топливный фильтр располагается в топливопроводе за пределами
топливного бака, но он может также интегрироваться в модуль внутри топливного
бака.
В осаждении загрязняющих
веществ в форме твердых частиц, наряду с эффектом просеивания, принимают
участие также эффекты столкновения, диффузии и блокировки.
В качестве фильтрующей
среды получила распространение гофрированная бумага, частично со специальной
пропиткой. Она размещается в топливной системе таким образом, что скорость
потока топлива через все секции поверхности фильтрующей среды поддерживается
максимально возможно одинаковой.
Срок службы традиционных
фильтров последовательного расположения, в зависимости от объема фильтра,
составляет от 60 до 90 тыс. км пробега. Для фильтров, встроенных в топливный
бак, гарантируется срок службы 160 тыс. км пробега.
Корпус фильтра
изготавливается на выбор из стали, алюминия или синтетики. Он имеет резьбовые,
шланговые или быстродействующие соединения.
Эффективность фильтра
зависит от направления движения потока. Поэтому при замене фильтров последовательного
расположения обязательно должно соблюдаться направление потока, указанное стрелкой
на корпусе.
Регулятор
давления топлива
Регулятор давления топлива
устанавливает в топливной системе давление определенной величины, возвращая
избыточное количество поданного топлива по рециркуляционному топливопроводу обратно
в топливный бак.
В топливных системах с
рециркуляцией регулятор давления топлива, как правило, установлен на топливной
рампе. Воздушная трубка, которая ведет к впускному трубопроводу, создает
постоянную разность в давлениях между форсунками и впускным трубопроводом.
В топливных системах без
возвратного трубопровода постоянное давление в системе подачи топлива
поддерживается относительно атмосферного. Изменяющаяся разность между давлением
топлива и давлением во впускном трубопроводе требует ввода коррекций при
расчете времени впрыска. В этих системах регулятор давления топлива 4 (рис.147)
встроен в топливный бак.
Топливная
рейка
Топливо, поданное насосом,
поступает в топливную рейку (9, рис.137), на которой закреплены форсунки.
Наряду с форсунками, на
топливной рейке чаще всего закреплены также регулятор давления топлива и,
возможно, демпфер давления.
В зависимости от
требований, предъявляемых к различным типам автомобилей, топливная рейка изготавливается
из высококачественной стали или пластмассы. Для испытаний в условиях автомастерской
в топливную рейку может быть встроен диагностический клапан.
Электромагнитные
форсунки
Электромагнитные форсунки
(10, рис.137) входят во впускной трубопровод таким образом, что струя впрыска
попадает в зону перед тарелкой или непосредственно на тарелку впускного клапана
(в некоторых случаях также на несколько впускных клапанов). Здесь во впускном
трубопроводе топливо вместе со всасываемым воздухом образует горючую смесь.
Каждый цилиндр снабжен форсункой.
Электромагнитные форсунки
(рис.148) состоят в основном из:
·
корпуса 9 с электрическим 8 и
гидравлическим 1 соединительными разъемами;
·
обмотки электромагнита 4;
·
подвижного игольчатого клапана 6 с
якорем соленоида и запорным сферическим элементом;
·
седла 10 клапана с распылительной
пластиной (с отверстием) 7 для впрыскивания топлива;
·
пружины 5.
Для обеспечения
бесперебойной работы форсунки те ее части, которые контактируют с топливом, изготовлены
из нержавеющей стали. Фильтровальная сетка 3 в приемном канале форсунки защищает
ее от загрязнений, содержащихся в топливе.
В используемых в настоящее
время форсунках подача топлива осуществляется по оси форсунки сверху вниз.
Топливопровод закреплен на гидравлическом соединительном разъеме 1 с помощью специального
зажимного устройства. Крепежные хомуты обеспечивают надежную фиксацию. Уплотнительное
кольцо 2 на гидравлическом соединительном разъеме позволяет герметично
соединить форсунку с топливной рейкой.
Форсунка имеет
электрическое соединение с блоком управления двигателем.
Когда соленоид форсунки
обесточен, пружина и усилие, возникающее за счет давления топлива, прижимают
иглу клапана с запорным сферическим элементом к седлу клапана конической формы.
За счет этого система подачи топлива герметизируется относительно впускного
трубопровода. Когда на обмотку подается напряжение, за счет тока возбуждения
возникает электромагнитное поле, которое притягивает якорь иглы клапана.
Запорный сферический элемент приподнимается над седлом клапана, и происходит
впрыскивание топлива. Когда ток возбуждения выключается, игла клапана, за счет
усилия пружины, снова опускается на седло, закрывая форсунку.

Рисунок
148 – Конструкция электромагнитной форсунки EV6:
1 –
гидравлический разъем; 2 – уплотнительное кольцо; 3 – фильтр; 4 – обмотка
электромагнита; 5 – пружина; 6 – игла клапана с якорем и запорным сферическим
элементом; 7 – распылительная пластина с отверстиями для впрыскивания топлива;
8 – электрический соединительный разъем; 9 – корпус форсунки; 10 – седло
клапана
Распыление топлива
осуществляется через одно или несколько отверстий в распылительной пластине. С
помощью этих отверстий достигается точное постоянство впрыскиваемого количества
топлива. Распылительная пластина с отверстиями исключает образование осадков
топлива. Форма струи распыливаемого топлива зависит от расположения и числа
этих отверстий.
Хорошая герметичность
клапана в области седла обеспечивается за счет принципа уплотнения конус/
сферический элемент. Форсунка устанавливается в предусмотренное для этого
отверстие во впускном трубопроводе. Нижнее уплотнительное кольцо служит для
герметизации форсунки относительно впускного трубопровода. Количество топлива,
впрыскиваемого за единицу времени, в основном определяется:
·
давлением в системе подачи топлива;
·
противодавлением во впускном
трубопроводе;
·
геометрией зоны выхода топлива.
4.Элементы
системы зажигания
Катушка
зажигания
Катушка зажигания
накапливает энергию зажигания, необходимую для воспламенения рабочей смеси, и
генерирует высокое напряжение (потребное напряжение зажигания), необходимое для
создания искрового разряда на свече зажигания.
В системе М-Мотроник
катушка зажигания (12, рис.137) крепится непосредственно к свече зажигания.
Речь идет о системе зажигания с так называемым неподвижным распределением
зажигания и об одноискровых катушках зажигания, обслуживающих каждый цилиндр,
обеспечивая генерирование высокого напряжения. Распространены также системы с
двухискровыми катушками зажигания, в которых две свечи зажигания обслуживаются
одной общей катушкой зажигания. Системы только с одной катушкой зажигания
требуют применения распределителя высокого напряжения с механическим вращающимся
ротором. В современных системах зажигания эти типы распределения уже не применяются.
Свечи
зажигания
Свеча зажигания за счет
образования искрового разряда между электродами воспламеняет рабочую смесь,
находящуюся в цилиндре.
5.Элементы
системы очистки отработавших газов
Трехкомпонентный
каталитический нейтрализатор отработавших газов
Этот нейтрализатор преобразовывает образующиеся в
результате сгорания рабочей смеси токсичные вещества – оксид углерода СО, углеводороды
СН и оксиды азота NOX в водяной пар H2O, азот N2 и углекислый газ СО2.
Лямбда-зонды
Лямбда-зонд (20, рис.137)
измеряет содержание кислорода в отработавших газах и таким образом позволяет
сделать выводы о составе рабочей смеси в цилиндрах двигателя. Блок управления
двигателем использует сигнал лямбда-зонда, для того чтобы иметь возможность
поддерживать стехиометрическое соотношение топлива и воздуха в смеси (a = 1). При таком
составе смеси трехкомпонентный каталитический нейтрализатор обладает максимальной
эффективностью очистки отработавших газов от токсичных веществ.
В системах М-Мотроник
используются исключительно двухточечные лямбда-зонды. В зависимости от системы,
за нейтрализатором отработавших газов может устанавливаться дополнительный лямбда-зонд
(33, рис.137), что повышает эффективность очистки отработавших газов и
обеспечивает контроль за старением каталитического компонента нейтрализатора.
Система
подачи дополнительных порций воздуха
Кратковременная подача
воздуха в выпускной коллектор после пуска двигателя приводит к добавочному
сгоранию несгоревших углеводородов (СН), содержащихся в отработавших газах. Эта
мера снижает эмиссию углеводородов. С другой стороны, она сокращает время
нагревания каталитического нейтрализатора, и он быстрее достигает своей рабочей
температуры.
Этот (дополнительный)
воздух нагнетается вспомогательным насосом (4, рис.137). При этом подающий
воздухопровод при неработающем насосе перекрыт клапаном подачи дополнительного
воздуха (5, рис. 1). Для этого блок управления двигателем управляет работой
обоих элементов.
6.Рабочие
характеристики
Наряду с уже
упоминавшимися датчиками, рабочие характеристики регистрируются еще целым рядом
дополнительных датчиков. В качестве примера можно привести:
·
датчик частоты вращения коленчатого
вала (22, рис.137) для определения положения коленчатого вала и расчета частоты
вращения коленчатого вала двигателя;
·
фазный датчик (13, рис.137) для
определения положения фазы (т.е. фазы рабочего цикла двигателя) распределительного
вала;
·
датчики температуры охлаждающей
жидкости (19, рис.137) и температуры всасываемого воздуха для расчета поправок,
зависящих от этих значений температуры;
·
датчик детонации (18, рис.137) для
определения детонации двигателя.
Датчик
частоты вращения коленчатого вала
Датчики частоты вращения
коленчатого вала двигателя используются для:
·
измерения частоты вращения коленчатого
вала двигателя;
·
определения положения коленчатого вала
(или положения поршней двигателя).
Частота вращения
коленчатого вала рассчитывается по частоте сигналов, поступающих от этого датчика.
Выходной сигнал датчика является одной из важнейших величин электронной системы
управления двигателем.
Датчик установлен
оппозитно ферромагнитному триггерному колесу 7 (рис.152), от которого он отделен
воздушным зазором.

Рисунок
152 – Индуктивный датчик частоты вращения коленчатого вала:
1 –
постоянный магнит; 2 – корпус датчика; 3 – блок цилиндров двигателя; 4 –
полюсный штифт; 5 – обмотка; 6 – воздушный зазор; 7 – триггерное колесо с
зазором-меткой
В датчике находится
сердечник 4 из электротехнического железа (полюсный штифт), окруженный обмоткой
5. Полюсный штифт соединен с постоянным магнитом 1. Магнитное поле воздействует
на этот полюсный штифт и поступает на триггерное колесо. Уровень магнитного
потока, проходящего через обмотку, зависит от положения датчика относительно
триггерного колеса (зазор или зуб). Магнитный поток рассеяния концентрируется
на зубе, что ведет к усилению полезного потока, проходящего через обмотку. Напротив,
зазор ослабляет этот поток. При вращении триггерного колеса происходит
изменение магнитного потока, что, в свою очередь, индуцирует в обмотке
электромагнита синусоидальное выходное напряжение (рис.153), пропорциональное
скорости изменения этого потока и, следовательно, частоте вращения коленчатого
вала. Амплитуда напряжения переменного тока сильно возрастает по мере повышения
частоты вращения триггерного колеса (от нескольких мВ до значений > 100 В).
Для генерирования сигнала достаточного уровня необходима частота вращения
величиной как минимум 30 об/мин.
Количество зубьев
триггерного колеса зависит от условий его применения. В системах управления
двигателем с регулированием с помощью электромагнитных клапанов обычно
используются триггерные колеса с 60-ю зубьями, при этом два зубца пропущены
(7,рис. 152).Следовательно, это колесо имеет 60 - 2 = 58 зубьев. Очень большой
зазор между зубьями предназначен для отметки определенного положения коленчатого
вала и служит как установочная метка для синхронизации блока управления.

Рисунок
153 – Характеристика сигналов индуктивного датчика частоты вращения коленчатого
вала:
1 –
напряжение при прохождении зуба; 2 – напряжение при прохождении зазора; 3 –
напряжение при прохождении зазора-метки
В другом варианте
исполнения триггерного колеса имеется всего по одному зубу на каждый цилиндр
двигателя. Например, в четырехцилиндровом двигателе это четыре зуба, т. е. за
один оборот этого колеса генерируются четыре импульса.
Геометрические размеры
зубьев и полюсов должны соответствовать друг другу. Электронная схема оценки
данных в блоке управления преобразует синусоидальное напряжение с очень разной
амплитудой в прямоугольное напряжение с постоянной амплитудой. Этот сигнал
подвергается обработке в микроконтроллере блока управления.
Фазный
датчик Холла
Частоты вращения
распределительного и коленчатого валов соотносятся как 1:2. Положение распределительного
вала показывает, находится ли поршень двигателя, движущийся к ВМТ, на такте сжатия
или выпуска. Фазный датчик на распределительном валу передает эту информацию в
блок управления.
В таких датчиках (рис.154,
а) использован эффект Холла. Вместе с распределительным валом вращается
ферромагнитное триггерное колесо 7 с зубьями и сегментами, либо диафрагма с
отверстиями. Интегральная схема датчика Холла 6 располагается между триггерным
колесом и постоянным магнитом 5, который генерирует магнитное поле, перпендикулярное
элементу Холла.
Когда зуб Z триггерного
колеса проходит у токонесущего элемента (полупроводниковая плата) стержневого
датчика, то он изменяет напряженность магнитного поля, перпендикулярного
элементу Холла. В результате этого путь электронов, которые движутся за счет
продольного напряжения, действующего на элемент, отклоняется по перпендикуляру
к направлению тока.

Рисунок
154 – Фазный датчик Холла:
а
– расположение датчика и однодорожечного триггерного колеса относительно друг
друга; б - характеристика выходного сигнала UA
1 –
электрический разъем; 2 – корпус датчика; 3 – блок цилиндров двигателя; 4 –
уплотнительное кольцо; 5 - постоянный магнит; 6 – интегральная схема Холла; 7 –
триггерное колесо с зубом/ сегментом Z и
зазором L; a воздушный зазор; a - угол
поворота; jS – ширина сигнала; UA – выходное напряжение
За счет этого возникает
сигнал напряжения (напряжение Холла), который находится в милливольтовом
диапазоне и не зависит от относительной скорости между датчиком и триггерным
колесом. Оценивающая электронная схема, встроенная в интегральную схему,
вырабатывает сигнал в форме прямоугольных импульсов (высокий/ низкий, рис.154,
б).
Пьезоэлектрический
датчик детонации двигателя
Датчики детонации по
принципу своего функционирования являются датчиками вибрации и пригодны для
регистрации акустических колебаний, возникающих в конструктивных элементах двигателя.
Эти колебания возникают при неконтролируемом детонационном сгорании в рабочей
смеси в двигателе. Они преобразуются датчиком в электрические сигналы и
направляются в блок управления. Как правило, 4-цилиндровые рядные двигатели
оснащены одним датчиком, 5- и 6-цилиндровые двигатели – двумя, 8- и 12-цилиндровые
двигатели – двумя и большим числом датчиков. Они подключаются в соответствии с
порядком зажигания.
Любая масса, благодаря
своим инерционным свойствам подвергающаяся воздействию колебаний, создает
усилия сжатия на кольцеобразном пьезокерамическом элементе 1 (рис.156) такой же
частоты, как и возбуждающие колебания. Внутри керамического элемента эти силы
сжатия вызывают сдвиг заряда на внутренних сторонах керамического элемента. При
этом возникает электрическое напряжение, которое снимается контактными дисками
5 и далее поступает в блок управления для обработки этого сигнала.
Чувствительность датчика
определяется значением выходного напряжения, приходящегося на единицу ускорения
(мВ/ г) на выходе датчика. Напряжение оценивается высокоомным усилителем переменного
тока в блоке управления системы зажигания или в системе управления двигателем.

Рисунок
156 – Датчик детонации:
1 –
пьезокерамический элемент; 2 – сейсмическая масса с усилиями сжатия F; 3 – корпус; 4 – затяжной болт; 5 - контактная поверхность;
6 – электрическое соединение; 7 – блок цилиндров двигателя; V - вибрация
Место установки датчика
детонации в каждом двигателе выбирается таким образом, чтобы можно было надежно
определить детонацию в каждом цилиндре двигателя. Чаще всего датчик крепится на
винтах на боковой стороне блока цилиндров двигателя. Для того чтобы
результирующие сигналы вибрации в конструктивных элементах могли передаваться
на датчик от места измерения на блоке цилиндров двигателя без резонанса и в
соответствии с выбранной характеристической кривой, следует учесть следующие
факторы:
·
крепежный болт должен затягиваться
определенным моментом затяжки;
·
контактная поверхность датчика и
отверстие в блоке цилиндров двигателя должны соответствовать определенным требованиям
по качеству;
·
не должны применяться шайбы любого
типа.
|